Introduction
With the phenomenon of global warming and tree felling, the Earth’s mother is experiencing a great hurt. People are making lots of pollution and exhausting the limited natural resources. However, people are realizing the great damage that they bring to the environment and have started to pay attention to protecting the earth. However, this is not an easy task. People nowadays are beginning to do small things around them to protect their living environment such as using recycled packages, sustainable objects and so on. Meanwhile, many businesses also start to contribute to the building of a greener environment by using eco-friendly resources during their production process. For example, Leisure Touch Rattan is dedicated to manufacturing environmentally-friendly materials including plastic rattan and plastic wood board to execute their social responsibility.
As an outdoor furniture supplier or an experienced retailer, you might be familiar with the two materials that I mentioned above. Although plastic wood does not have a long history in the furniture industry, it is commonly used in the production of outdoor furniture because of its excellent functionality and aesthetics. However, at this time, some suppliers might still be confused about what exactly plastic wood board is and why it is so popular. In the following paragraphs, I will explain this material to you to help you understand this material clearly!
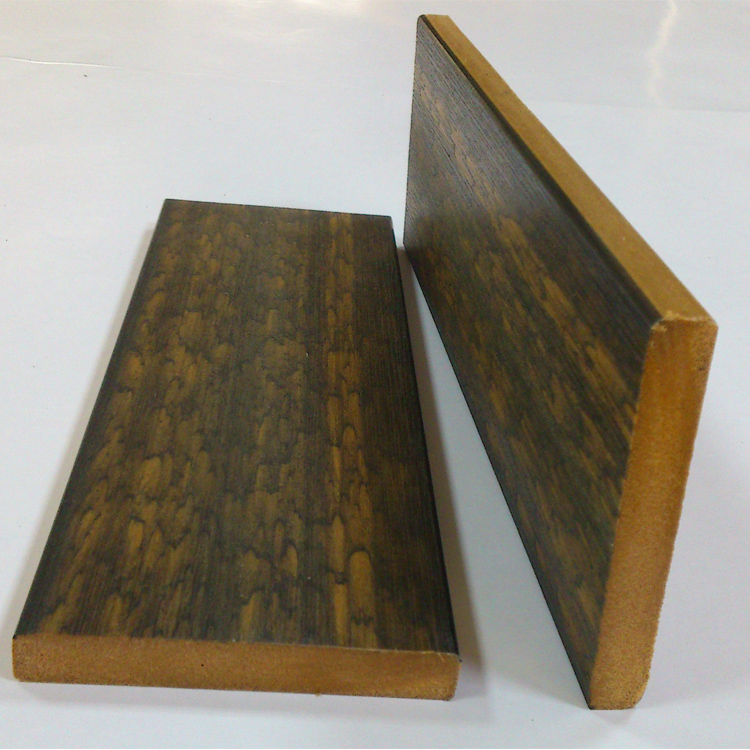
What Is Plastic Wood?
Plastic wood, also called plastic lumber or synthetic wood, is not a kind of fresh material for most outdoor furniture manufacturers. It is nowadays commonly used in the production of outdoor furnishing because of its excellent characteristics. Many people have started to choose plastic wood as a perfect substitution for traditional real wood, which is more eco-friendly, price effective and durable than natural wood. Plastic wood is normally made from a blend of recycled plastic materials, such as high-density polyethene (HDPE), polystyrene (PS), or polyvinyl chloride (PVC) with additives for enhancing strength and stability. At this time, some people might be curious about how it can compare with real wood. Plastic lumber is made with the natural look of real wood which imitates the natural grains and textures of it. If you just look at furniture that is made of plastic lumber, you might not clarify if it is real wood or not since they are highly similar in appearance.
At this point, I need to clarify one important thing. That is, the plastic wood board is not a wood-plastic composite (WPC). They are different in terms of their manufacturing process. However, many people or even outdoor suppliers might mess up these two materials. The plastic wood that I am discussing in this article is made of plastics, by contrast, while producing wood-plastic composite, it contains some real wood chips inside, making it not as durable outdoors as plastic lumber. When people are selecting a suitable material for outdoor furniture, I would say the plastic wood board is one of the top choices since it has strong resistance to harsh weather conditions outdoors such as long-time sunshine exposure, heavy wind and rain. It can survive a long time in highly humid conditions and will not break because of corrosion. As a result, people do not need to worry about it and pay too much attention to the cleaning process of plastic wood outdoor furniture.
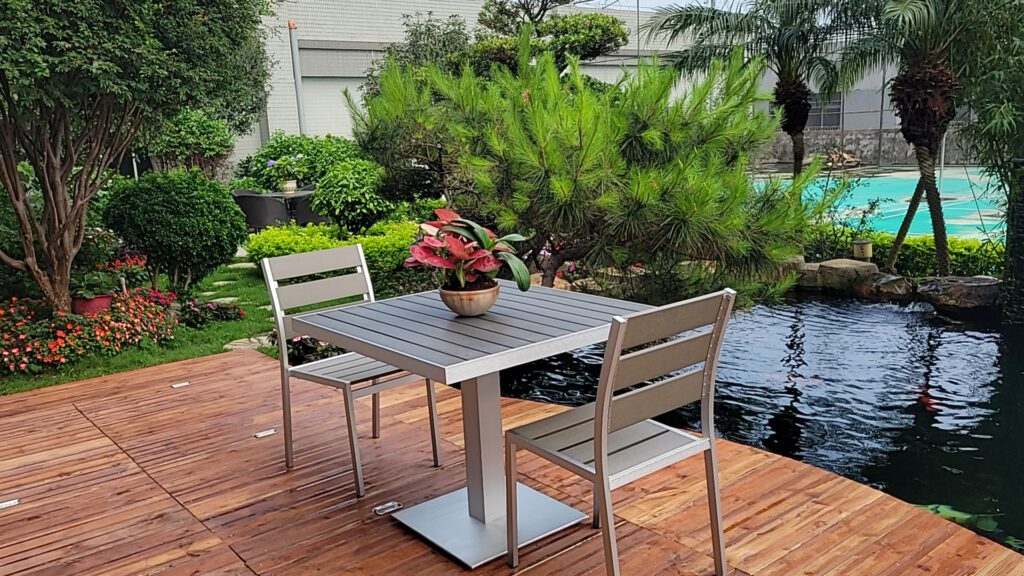
6 Production Processes of Plastic Lumber
Before we talk about the various types and styles of plastic lumber, let’s talk about LTR’s manufacturing processes of this material first so that you will have a more comprehensive knowledge of this sustainable outdoor furniture material.
Step 1: Material Preparation
In this step, what LTR needs to do is to mix and blend the needed materials together to produce plastic lumber. This process includes harmonizing a selection of important raw materials such as HDPE, PS, and antioxidants. These raw materials are carefully measured and mixed according to LTR’s special production recipe, guaranteeing accuracy and uniformity throughout the whole manufacturing process.
Step 2: Extrusion Process
This process is about shaping the plastic wood boards into the ideal shapes by controlling the temperature. After the first material mixing process, the mixture is fed into an extruder. The extruder heats the mixture to a high temperature, and the melted mixture is then forced through a die to form the shape of a board. The extruded board is then cooled using a water bath to solidify it.
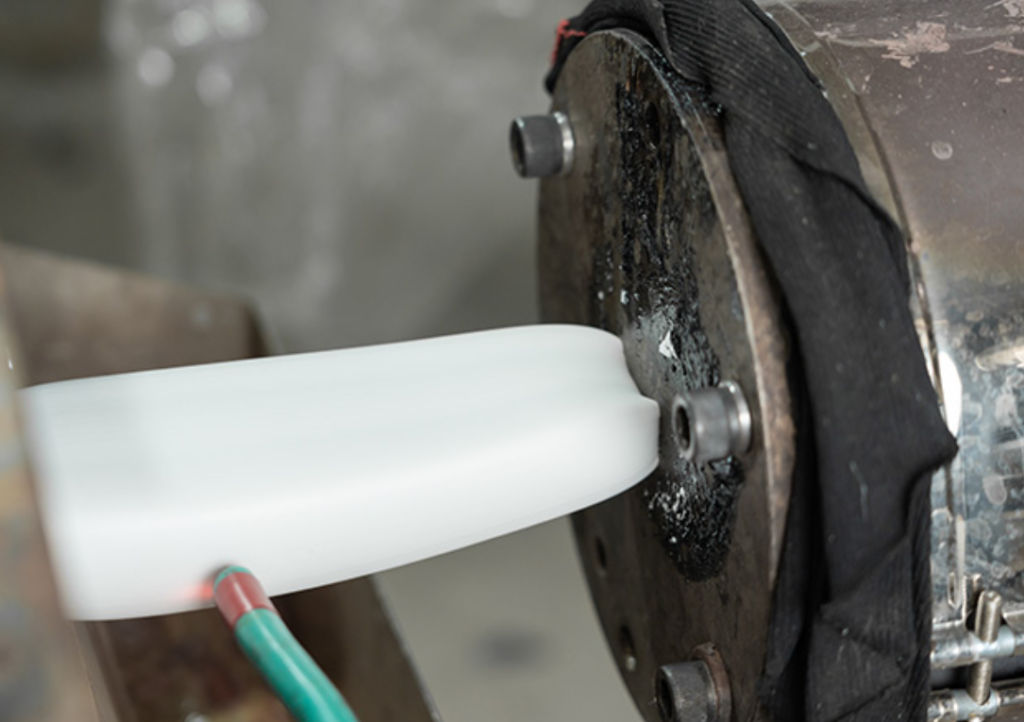
Step 3: Molding Process
This step is mainly to guarantee that the plastic wood boards are in the same specification. They use a hydraulic press to press and shape the boards to keep them in a consistent shape that customers need.
Step 4: Size Treatment
During this step, flatting and cutting processes happen. High-pressure automatic machines are used to flatten the plastic wood boards. In this cutting process, lots of advanced cutting tools such as CNC machines, drills, and saws are involved to cut the desired size of the boards.
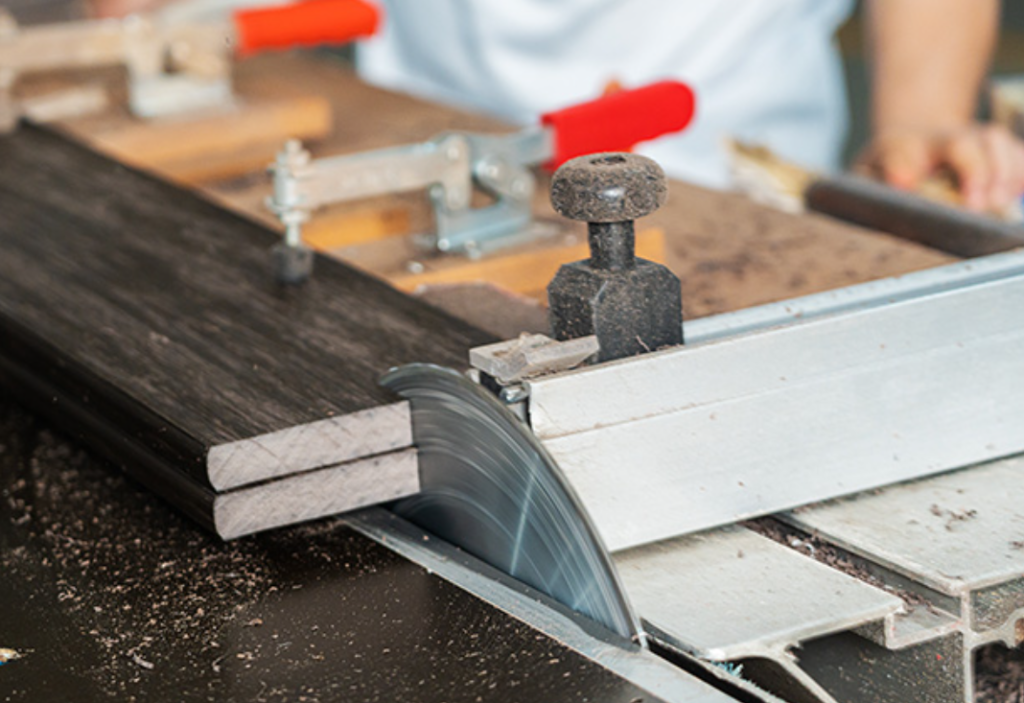
Step 5: Surface Treatment
This step is to complete the brushing and embossing surface treatment of the boards to improve the appearance and durability of the material. With decades of sophisticated experience in manufacturing plastic wood, LTR offers a wide range of surface treatments, including embossing, polishing, and sanding to enhance the smoothness and attractiveness of the surfaces. Besides, this step can also improve plastic wood boards’ resistance to scratches and stains.
Step 6: Final Packing Process
This last step is to pack the materials and make them ready to be shipped. At this stage, a layer of strong protection is used to cover and protect the plastic wood boards so that customers can get their products in perfect condition after shipping. In this step, the boards are carefully stacked and wrapped in cartons with a protective PE foam cover, making sure that plastic wood boards are delivered to their destination promptly.
LTR’s Five Different Craftsmanship of Plastic Wood Board
As one of the most popular outdoor furniture materials, it can be produced in many different kinds of final boards based on what customers want. However, manufacturing various exquisite and high-quality plastic wood boards is not an easy task. Different craftsmanship requires the professional skills of the supplier. Now, I will introduce five different excellent craftsmanship that LTR has. You can also browse the website for more customization options.
1. One-Sided Plastic Wood
Just like the name, this kind of plastic wood board has a uniform colour inside and outside the material. During the production process, LTR needs to maintain a consistent single colour for the whole board, presenting a uniform appearance across the entire wood board.
2. Binding Skill
This skill is similar to the one-sided effect; it also has one single colour if you just look at the outer surface of the boards. However, the difference is that the outer and inner parts of the plastic wood board have two different colours, separating the colours of the two sectors.
3. Thermal Printing Style
LTR’s thermal printing skill allows for the application of a layer of the customized membrane with different patterns on a single side or all sides of the plastic wood boards, which can perfectly satisfy what your customers want for the patterns of wood boards.
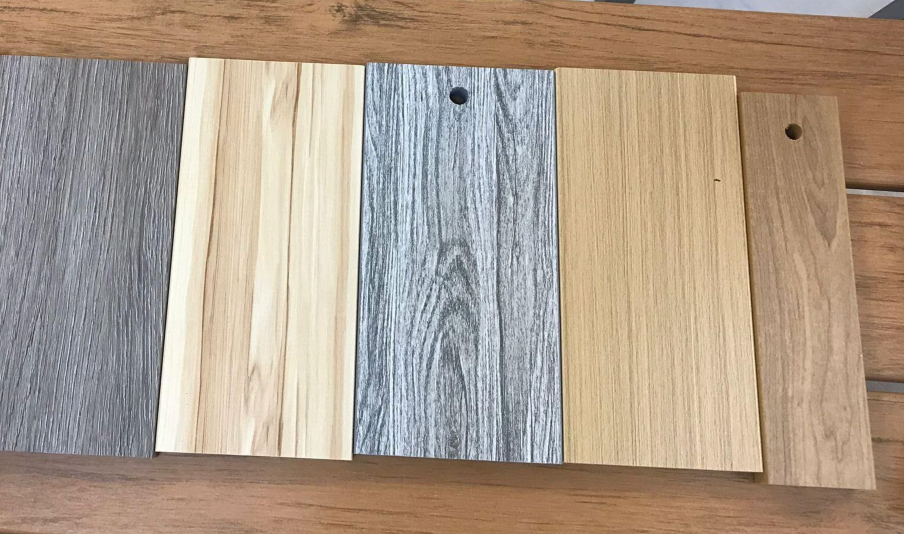
4. Colour Matrix Style
This craftsmanship can make the plastic wood boards look like the natural wood the most. People who would like to chase the natural appearance of real wood but want the durable functionality of plastic wood boards will opt for this style. That is because this style is crafted with irregular lines and grains, maintaining the natural and pure conditions of real wood
5. Printing Style
This craftsmanship is similar to the thermal printing skill that I mentioned above since they are also designed for creating customization patterns on plastic wood boards. However, they are different in the manufacturing process. This skill allows for more personalized effects compared to thermal transfer methods. Direct printing of different patterns and effects can be made on plastic wood board directly, which seamlessly integrates patterns and the wood board, resulting in a softer texture than thermal printing.
Four Exquisite Surface Styles of Plastic Wood Board
After discussing LTR’s various kinds of special craftsmanship of plastic wood boards, it is time to talk about the different types of surface effects of plastic wood. With these surface effects, furniture that is made of these plastic lumbers will look more charming and leave a stronger impression on people.
For this style, in order to achieve the natural look of the plastic wood board, a special manufacturing technique is applied on the boards to imitate the natural gains and texture of real wood by embossing. As a result, if you touch the plastic wood board with an embossing technique, you will feel that it is touched like natural wood.
The brushing technique is a type of skill that LTR uses to make their plastic wood boards look more real and natural. While manufacturing, the plastic wood boards are brushed by the machines to create a special brushing effect. If you touch the surface, you can feel some small wood flour on it. This craftsmanship is aimed at making the wood boards look more real and natural.
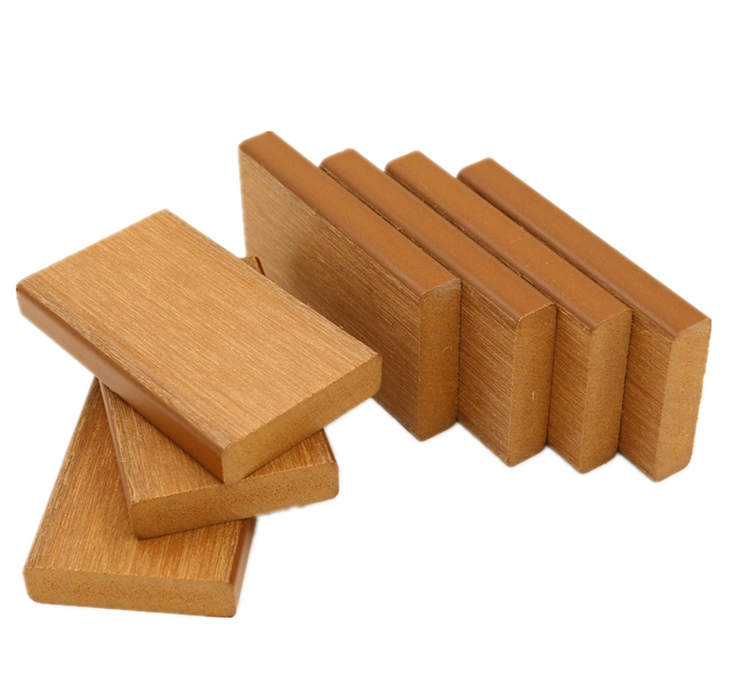
3. Planed Collection
For this type of collection, the plastic wood boards will have a flat and levelled surface. This is the most popular type in furniture production since it is simple but delicate. You can often see this kind of style in the applications of outdoor furniture such as tables, counters and chairs.
4. Polished Collection
This collection is to apply a layer of polished coating to the plastic wood boards which can make your furniture survive a long period outdoors. Since the layer of polished coating is just like additional protection for the boards, it can effectively preserve the natural patterns of plastic wood and make it shine in your comfortable outdoor areas.
Whether you are looking for an eco-friendly option, a versatile alternation to real wood, a long-lasting outdoor material or a cost-effective selection, LTR’s plastic wood boards can satisfy you with exquisite craftsmanship, excellent quality or personalized customization.
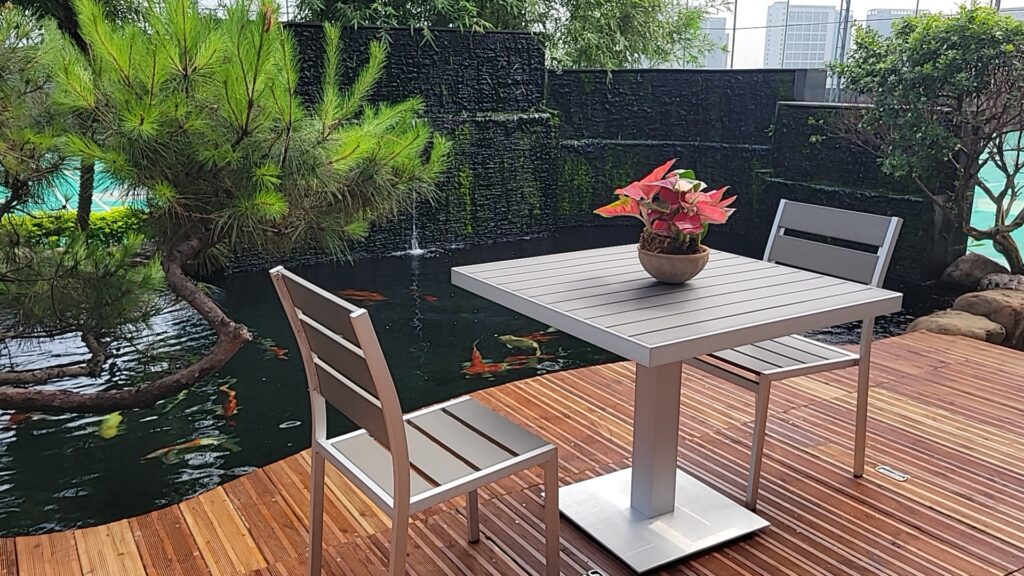
Conclusion
In general, with people’s increasing awareness of environmental protection, plastic wood has become a sustainable choice for most outdoor furniture suppliers due to its natural look, excellent practicability and various aesthetic craftsmanship. What is more, as a superior outdoor furniture material, it has lots of benefits that make it stand out among other materials. For example, its capability to survive for a long time in outdoor spaces is attractive to lots of outdoor lovers and manufacturers. Except for its resistance to harsh weather conditions, it does need additional care from people to maintain its original beauty. That is to say, it is not only practical but also convenient for customers. It can help people save more time to enjoy their comfortable, relaxing and joyful outdoor leisure instead of spending the whole time cleaning and maintaining the outdoor furniture. If you are interested in more detailed information and various craftsmanship of sustainable plastic wood boards, please check LTR’s website for more details!